振动与噪声抑制是机电工程系统设计及有限元分析不可忽视的环节。机电设备运转时的振动与噪声不只影响工作环境,还可能引发结构疲劳损坏。运用有限元软件进行模态分析,求解系统结构的固有频率、振型,预防共振现象。模拟设备运行时的动态激励,观察振动能量分布,锁定振动噪声源。据此在设计中优化结构刚度分布,添加阻尼材料或隔振装置,如在电机与基座间安装橡胶隔振垫,在高速旋转部件周边布置吸音材料。通过多手段协同,有效削减振动幅度、降低噪声水平,提升机电系统工作品质,符合人机友好环境构建需求。在海上风电安装工程中,吊装系统设计起着关键带领作用,分析塔筒、叶片吊装时的动态响应,保障安装精度。大型工装设计与制造
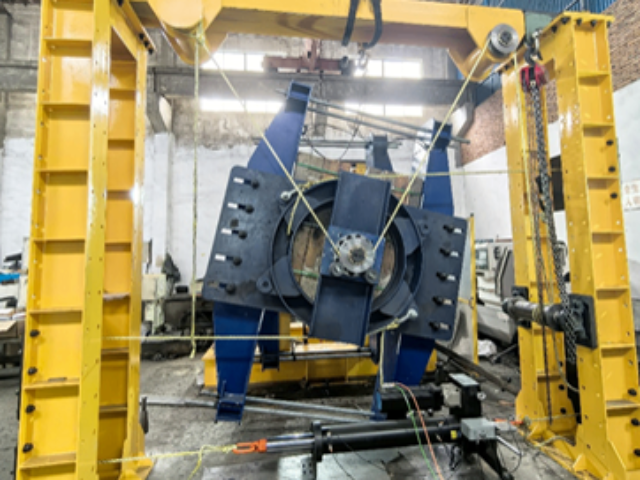
安全性设计是吊装称重系统的重中之重,有限元分析发挥关键作用。吊装过程涉及重物起吊、移动、降落,任何环节失误都可能酿成大祸。设计师利用有限元模拟不同工况下,如急停、加速、侧向冲击时,吊装结构的应力应变分布。针对关键受力部位,像吊索、吊钩、吊臂等,优化其结构设计,增强强度与刚度。考虑到可能的超载情况,模拟超载倍数下系统的承载极限,设置可靠的超载保护装置,一旦超重立即报警并限制起吊动作。此外,分析恶劣环境因素,如大风、低温对吊装系统力学性能的影响,提前采取防护措施,全方面保障吊装称重系统在复杂作业条件下的安全运行。大型工装设计与制造吊装系统设计利用云计算技术,加速复杂模型运算,短时间内获取多工况下吊装系统的应力、应变结果。
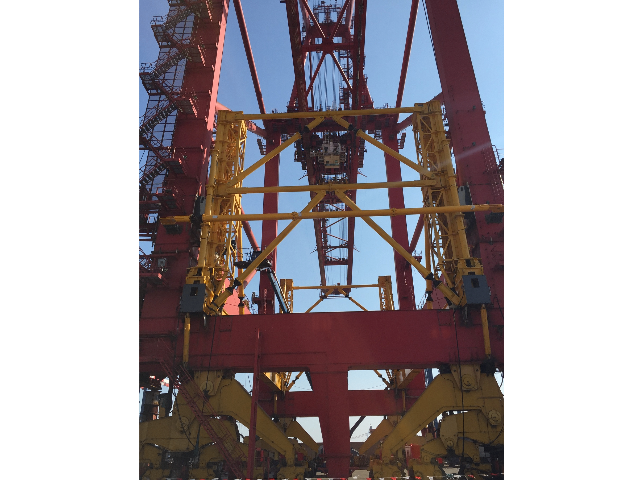
机械设计及有限元分析的起始点在于对机械结构的深入理解。设计师需依据机械的功能需求,全方面规划布局。从整体框架构建而言,要考量各部件的相对位置与连接方式,确保力的传递顺畅且稳定。在设计传动结构时,摒弃传统的经验式布局,运用机械原理知识,严谨分析不同传动比、传动方向对机械运行的影响,选定更优方案。有限元分析则在此基础上介入,针对关键承载部位,将其复杂几何形状离散化,模拟实际工况下的受力情况,查看应力、应变分布。依据分析结果,优化结构细节,如增厚高应力区材料、改变连接圆角大小,使机械结构从设计源头就具备高可靠性,能适应复杂多变的工作环境。
吊装翻转系统设计及有限元分析首要聚焦于翻转机构的精确设计。设计师需依据待翻转物体的形状、尺寸、重量分布等特性,精心规划翻转方式,是采用液压驱动的回转式结构,还是电动丝杆带动的翻转架。结合机械运动学原理,严谨推导翻转过程的运动轨迹,确保平稳、精确。有限元分析随即介入,针对关键的翻转连接部位与承载部件,将其复杂几何模型离散化,模拟不同翻转速度、角度下的受力状态,严密监测应力、应变变化。依据分析成果优化连接销轴尺寸、强化承载梁结构,使系统从初始设计就具备高度与稳定性,保障翻转作业安全、可靠地进行。吊装系统设计的自动化生产线设计充分考虑可扩展性,便于后续引入新技术、新设备,持续升级。
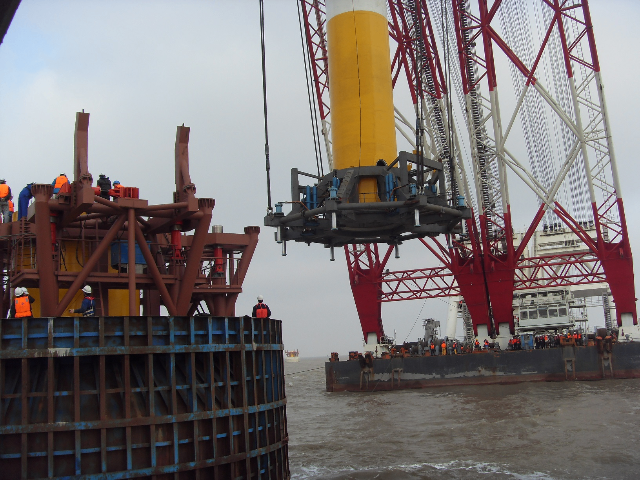
适应性拓展是非标机械设备设计及有限元分析的重点考量。鉴于非标设备应用场景多变,设计时要预留调整空间。比如在设计一台可用于多尺寸工件加工的设备时,机械结构采用模块化设计理念,将夹持、定位、加工等模块标准化,通过便捷的接口连接。有限元分析在此发挥作用,模拟不同尺寸工件加载下,各模块受力变形情况,优化模块刚度分配,确保在切换工件时,设备无需大改就能精确作业。同时,考虑设备可能面临的不同环境因素,如温度、湿度变化,模拟极端环境工况,提前调整材料选型与防护设计,让设备从容应对复杂多变的现实使用场景。吊装系统设计的持续推进将助力全球工程建设蓬勃发展,迈向更高水平的吊装作业新阶段。大型工装设计与制造
吊装系统设计在体育场馆大型钢结构吊装中,精确模拟施工过程中的风荷载影响,保障施工安全。大型工装设计与制造
智能决策算法优化是智能化装备的关键内核,有限元分析助力打磨。装备要依据采集的数据实时做出更优决策,传统算法难以应对复杂多变工况。设计师借助有限元分析软件模拟不同算法在各类场景下的运行效率、决策准确性。例如设计智能加工中心时,对比多种智能加工路径规划算法,通过有限元模拟加工过程,考量刀具磨损、加工精度、加工效率等因素,选定更佳算法。同时,结合机械结构特性,分析算法执行时对机械动作的控制精度要求,优化电机驱动、传动部件设计,确保机械动作能精确响应智能决策,全方面提升装备智能化水平。大型工装设计与制造
文章来源地址: http://swfw.huagongjgsb.chanpin818.com/qtswfw/deta_27452757.html
免责声明: 本页面所展现的信息及其他相关推荐信息,均来源于其对应的用户,本网对此不承担任何保证责任。如涉及作品内容、 版权和其他问题,请及时与本网联系,我们将核实后进行删除,本网站对此声明具有最终解释权。